Getting inland barge companies to replace wire towing cables with synthetic line is key for cordage companies that want to gain more traction in the towing market. But it can be difficult convincing companies to make the switch.
To start with, “riverboat operators may not be aware of this type of rope and the benefits and options they have,” said Garrett Krapf, regional account manager with Yale Cordage, Saco, Maine. He added that “change is difficult.”
The benefits of synthetic line include weight savings and usability. Synthetic line is seven times lighter per-diameter than wire and easier for deckhands to work with. There’s significantly less chance for injuries, and “that’s the big thing, back injuries and worker’s comp claims,” said Krapf. “One worker’s comp claim from a deckhand with injuries from throwing wire around can really hurt the company. It’s a lot easier to handle something that’s seven times lighter.” Additionally, synthetic line doesn’t rust or kink.
A company that switches from wire to rope has a learning curve. “You don’t want just a swap out,” Krapf said. Synthetic line compared to wire is soft and needs to be protected. Thus, winch drums, flanges, bollards, chalks, and whatever the wire has passed over and worn into needs to be inspected. Any sharp edges must be ground down and resurfaced, otherwise the line, especially when under a significant amount of tension, could fail.
For a towboat that’s about the worst thing that can happen. Then the towed vessel could suddenly go adrift, a line snaps back and severely injures or — worst-case scenario — kills a deckhand. Decreasing the chance for line failure was the impetus behind the introduction of Yale’s River Max and Samson Rope’s Icaria and IntelliTag.
River Max, a rebranded product, is still known as Mega Max in the industrial market. River Max was introduced to the workboat market last summer. It’s designed to take the place of chafing sleeves that protect a tow line from abrasion where there’s high wear potential, such as the edge of a barge.
River Max is a double-braided rope of ultrahigh molecular weight polyethylene (UHMWPE) fiber, with a diameter ranging from 5/8" to 1 ½" that covers up and protects 12-strand Ultrex line that’s the River Max’s load-bearing core. River Max is a core-dependent rope, meaning that 100% of the rope’s strength comes from the core — the 12-strand Ultrex line. The protective jacket doesn’t provide any line strength. It’s strictly there for abrasion protection.
When the River Max UHMWPE covering starts to wear though from abrasion, just strip the jacket off to repair or replace it. “The 12-strand Ultrex line should be in great shape,” said Krapf.
River Max works best taking the place of face and wing wires.
River Max “is a game changer,” Krapf said. Deckhands no longer have to change sections of chaffing on the line that might get hung up in the roller buttons or chalks. When barge tows being hooked up and moved around and there’s only short sections of chafing, that chafing must be positioned and then repositioned. But with River Max, the entire line is covered.
“You can save 10 to 15 minutes per hookup,” Krapf said. At the end of the day “that turns into hours and equals x amount of barges that can be moved. Each barge loaded is x amount of dollars.” Currently, River Max is in the trial stages with five or six riverboat companies.
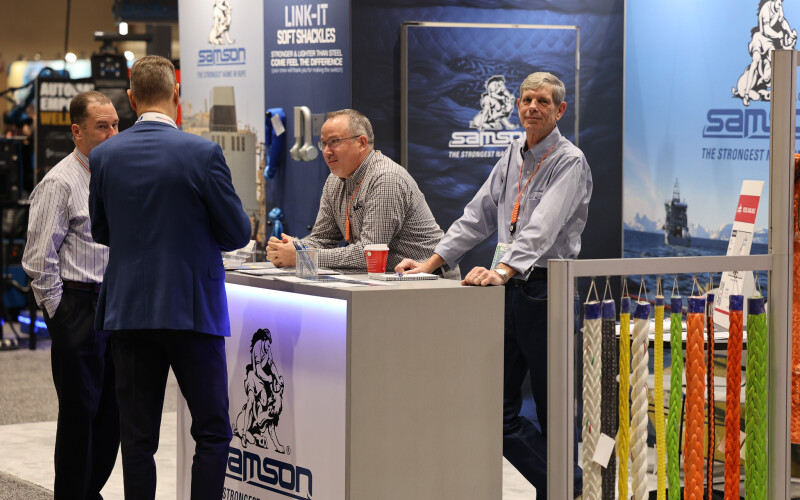
SAMSON ROPE
Avoiding towline failures begins with constantly monitoring the condition of the towline to ensure that it stays within an acceptable safety profile and is retired when it no longer fits that profile. By itself, a visual inspection isn’t enough to monitor whether a towing line stays within a certain safety profile.
Samson Rope’s Icaria, which brings the digital age to towline management, seems a good place to start moving beyond relying on visual inspections to track a line’s usage or measuring a line’s life expectancy based on the number of jobs or the hours or months it’s been in use.
Icaria was first introduced to the mooring industry about four years ago. Recently, Samson tailored Icaria to the line inspection needs of the workboat industry, for tracking and inspecting line “to determine when to retire a line before it breaks,” said Samson’s William Pernett.
It was introduced to the workboat market in June and is mostly being targeted at the ship-assist tug and riverboat markets on the Mississippi River, said Michelle Jarvis, Samson’s commercial marine product manager. “You can manage all your lines and inspections for all your vessels.”
Using a mobile app, Icaria lets you visually document a line’s inspection on deck. Then, a Samson service technician can review the inspection and “offer professional advice when there’s an issue or a problem,” said Pernett. The line inspection is automatically copied and sent to Samson. The tug’s captain or the fleet manager can access the same information.
Documenting a towline’s wear and any repairs that have been made provides a good idea of when a towline should be retired. “A lot of users have the potential of getting more life out of their rope, rather than just retire rope based on its operations,” said Pernett. Vessel owners have told him “that’s something they really like.”
Samson’s Icaria also has other line related programs. There’s a training platform that includes 12 courses related to line inspection, line installing, repairs and safety. “The classes are internet, video based,” said Jarvis, and there’s a course completion certificate from Samson. Operators can take the certificates “from vessel to vessel that shows their competency in line management.”
If you aren’t sure of a towing line’s condition or even what line it is, you can find out with Samson’s IntelliTag, which wraps around a towline and has radio frequency identification (RFID) capabilities. Just scan the IntelliTag with a mobile device that reads RFID — most smartphones do — then “you know what rope you are looking at, its diameter, strength, and certificate number,” said Pernett. Currently, all Samson vessel lines come with IntelliTag.
At the International WorkBoat Show in New Orleans in December, Samson showed off the latest generation of its Saturn-12, a 12-strand working line with sizes that range from 1⁄4"-dia. with an average strength of 8,600 lbs. to 3 1⁄2"-dia. with an average strength of 1.17 million lbs. Saturn-12 is made with Avient’s Dyneema SK78 fiber.
Previous Saturn-12 cordage had a black line for twist identification. The new Saturn-12 is distinctively two-toned orange and black, making it much easier to see if there’s a twist in the line. Any time there’s a twist in the line, the line’s strength is diminished.