Last month, WorkBoat hit the road on a shipyard tour across New England. WorkBoat’s national sales manager, Kristin Luke and I visited Senesco Marine to get an update on the shipyard's activity.
As Senesco Marine celebrates its 25th anniversary, it operates from a historic World War II (WWII) Naval Air Station. Many of the buildings used for vessel construction were originally aircraft maintenance hangars. The shipyard features a 1,200'x 80' WWII aircraft carrier pier with a depth of 28', as well as two large drydocks — the only two in Rhode Island.
Senesco is currently working on two hybrid ferries bound for the Maine coast, and two WindServe Marine LLC crew transfer vessels (CTVs). This month, the shipyard begins work on a 140'x50' deck barge, which they are building on spec with the intent to sell or charter in the future. This marks a new development for Senesco, as they are advancing in the commercial barge industry and can build to suit any customer's needs, the company noted. Additionally, Senesco handles routine and emergency repair work for many local ferry and barge companies, including the Steamship Authority, which oversees the Nantucket and Martha’s Vineyard ferries.
Additional insights gained highlighted Jones Act compliancy for hybrid ferries, as well as the Maritime Administration’s (Marad) Small Shipyard Grant Program being put into use. Last year, Senesco was awarded a $738,289 grant to support the purchase and installation of a one-sided sub arc welding system that consists of three integrated digital systems to load, fit, and weld multiple-plate panels, upgraded network servers and software, an all-terrain lift with variable reach, and a Tier 4 compressor.
Ted Williams, Senesco Marine’s president, spoke about the benefits of that grant and the sub arc welder as an asset to the yard.
“This machine runs a bead and can weld two (40'x40') plates together in about an hour and a half. It would take a human about three-to-four days to do it,” he said, highlighting where the better part of the grant was allocated,
“Most importantly we were awarded about half of a million dollars out of that grant to get a new head, that yellow head right there,” he said, pointing to the arc welder. “We’re going to replace that in a few months as that comes in. That’s an old analog system. We’re going to get a new digital system, which will make it even better, more accurate, and more refined.”
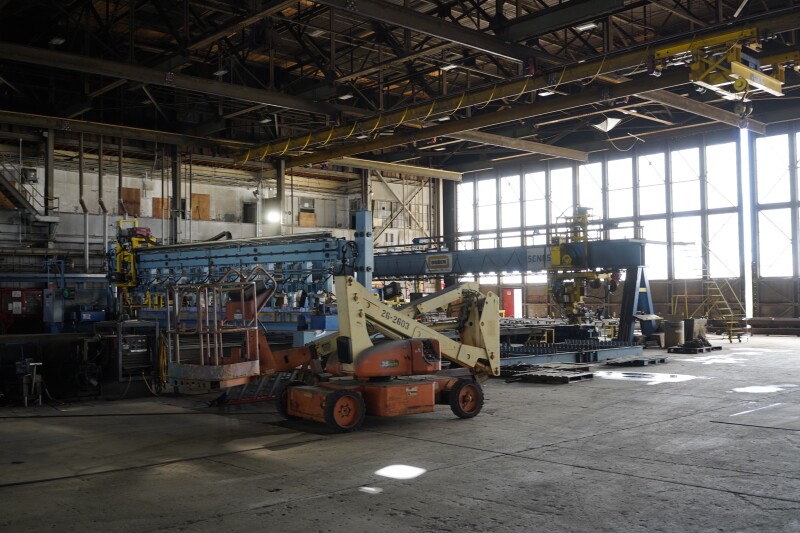
“This one’s capable of welding up to five-eighths of an inch thick. Whereas the new machine’s three-quarters to one-inch, so it allows us to weld thicker materials with less distortion.”
Williams emphasized the impact of the Marad program, “That's a great thing for shipyards to be able to tap into something like that and get that support.”
On the shipbuilding front, Senesco is currently working on the final two-of-six WindServe Marine CTVs. Last June, the shipyard launched the WindServe Genesis, which is currently providing crew transfer support at Ørsted's Southfork Wind project off the coast of Long Island before heading to work on the Revolution Wind project (R.I.), and Sunrise Wind (New York).
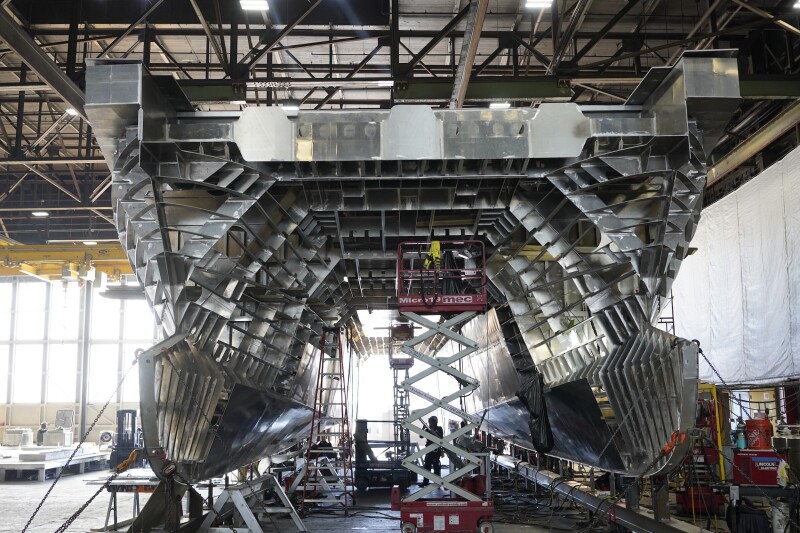
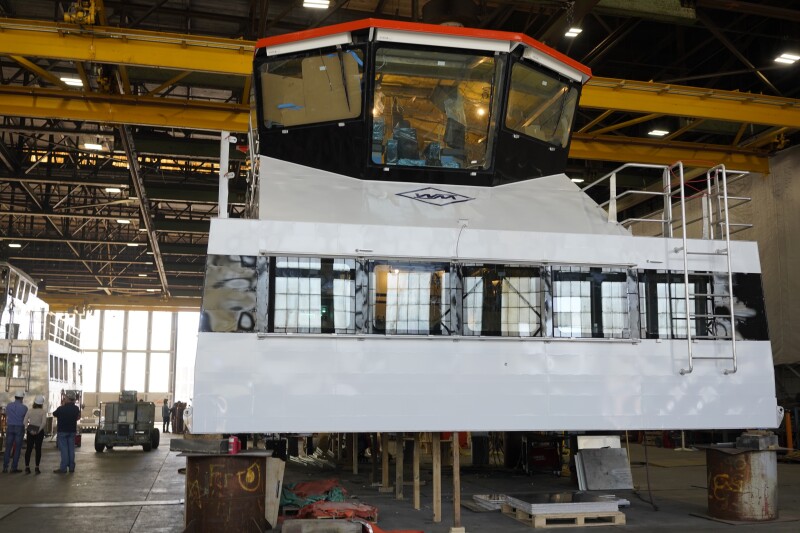
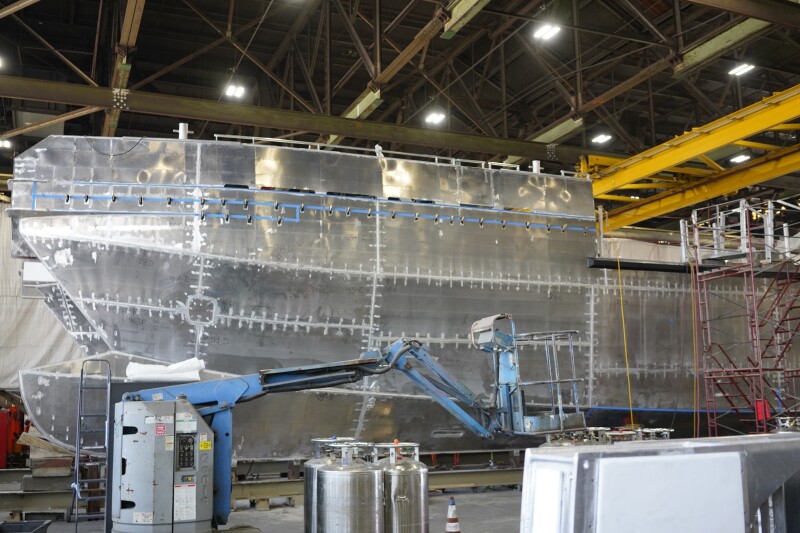
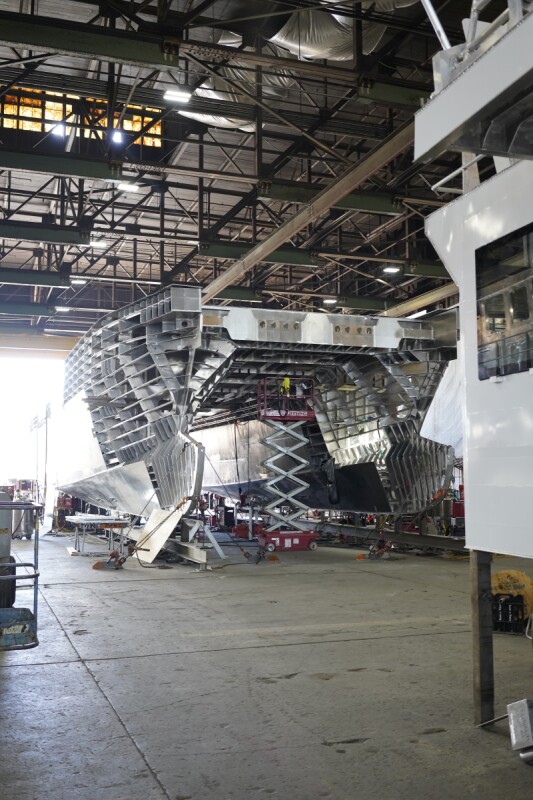
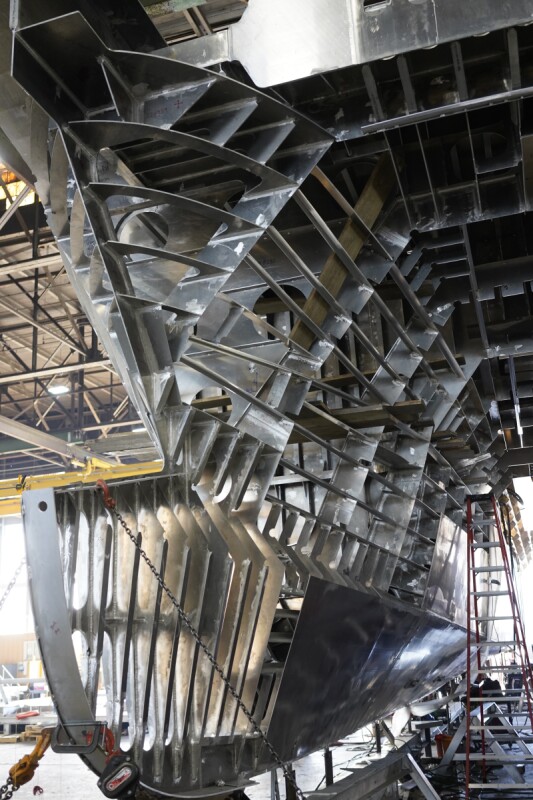
For the first four CTV builds — the Windserve Journey, Windserve Odessey, Windserve Explorer, and Windserve Genesis — all vessels measure 88.6'x29.5'x5.6' and can carry up to 24 offshore technicians. These aluminum catamarans were built with conventional Volvo Penta D13 main engines, each rated 690 hp at 2,300 rpm, and a Volvo Penta IPS 900 propulsion system. The vessels can achieve a service speed of 24 knots, with top speed capability of 27 knots.
For the final two CTVs currently under construction, the engine control rooms (ECR) have been pushed out an additional six feet to accommodate “hybrid-ready” battery capabilities. “We're not supplying the hybrid system at this time, but in the event a customer in the future wants that, there's enough room in the back of the engine room to go hybrid if there’s the desire to do that,” Williams noted.
Senesco uses Pierce Aluminum, Franklin, Mass., and Yarde Metals, Southington, Conn., for its aluminum parts. The shipyard's steel comes from Kloeckner Metals, Middletown, Conn. “We get all of the aluminum pre-cut, because we don’t want to contaminate steel and aluminum. Aluminum is really fickle. And if you get any steel dust in it, it will degrade the welds significantly.” Williams said.
On the ferry front, Senesco Marine is building a pair of hybrid ferries — one for the Maine State Ferry Service, and the other for the Casco Bay Island Transit District (CBITD or Casco Bay Lines), Portland, Maine. These vessels are the first-ever hybrid ferries in the Northeast.
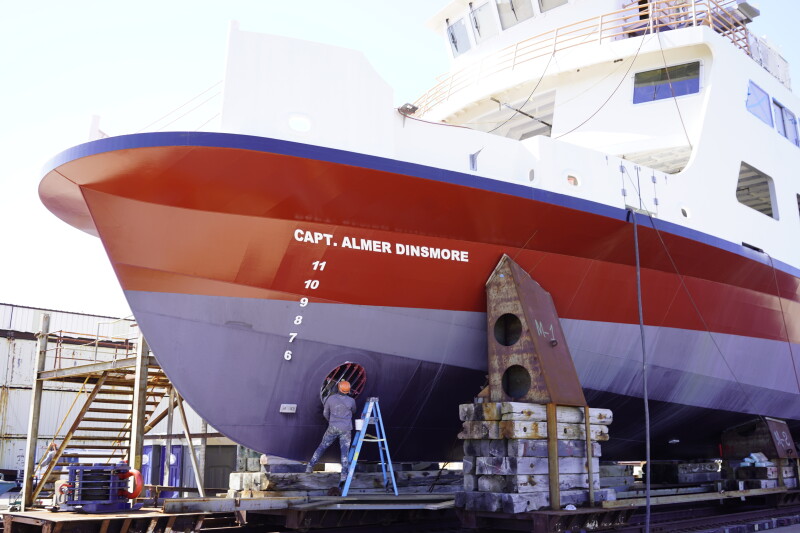
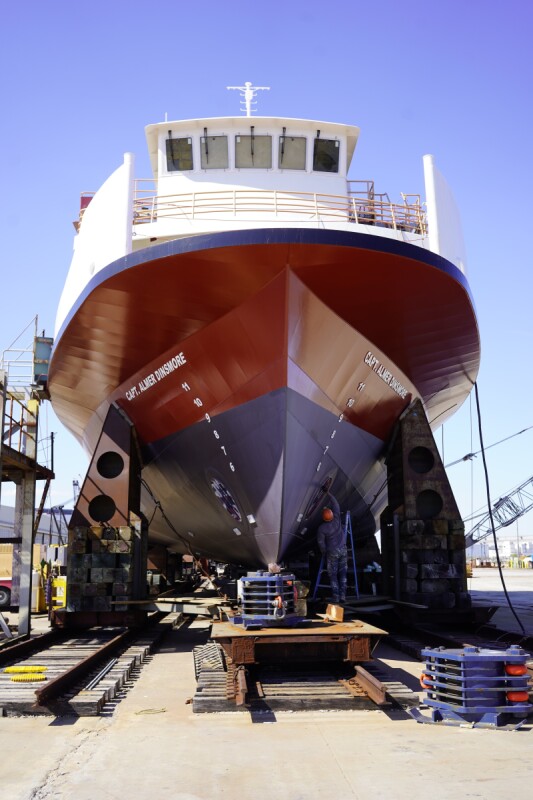
Pictured above is the Capt. Almer Dinsmore, designed by Gilbert Associates. The passenger vehicle ferry design has been created for the Maine DOT. The Dinsmore is a BAE Systems hybrid propelled sister vessel to the Captain Richard Spear, which was built in 2021. When complete, the vessel will be the first hybrid electric-powered passenger vehicle ferry to enter service in the state of Maine. The vessel is expected to be delivered later this year.
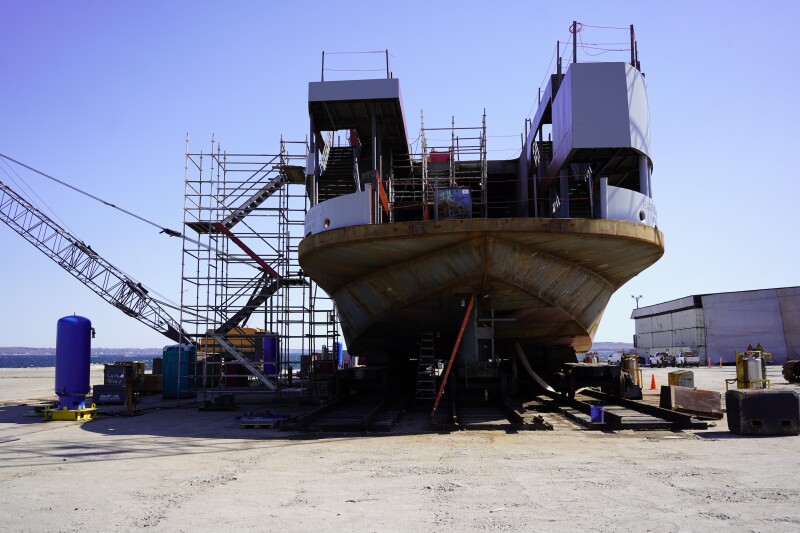
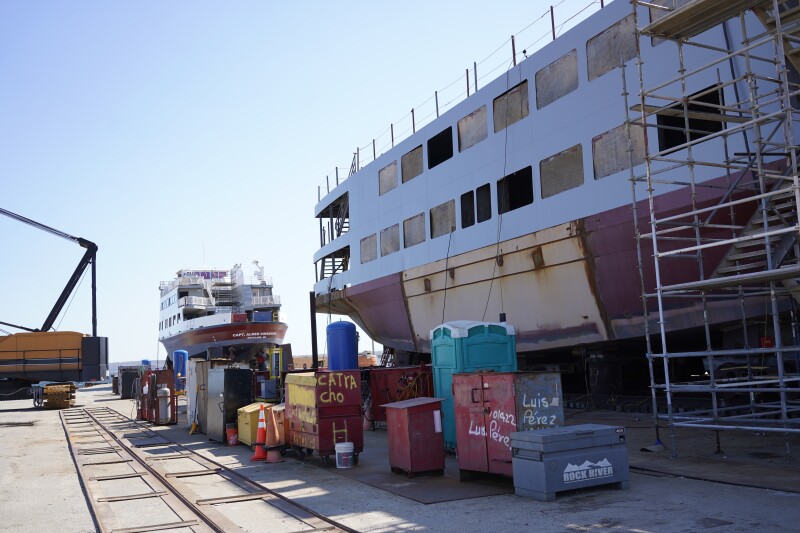
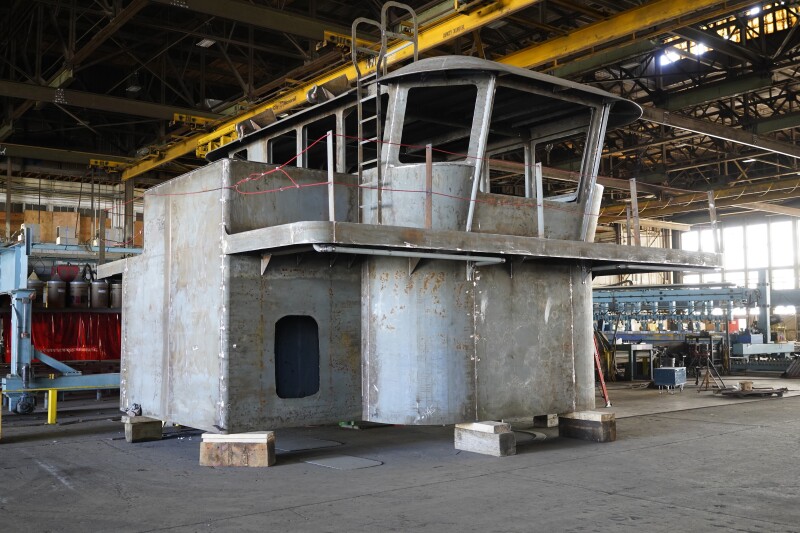
Additionally, CBITD is upgrading its fleet starting with a new $25 million double-ended, hybrid-electric ferry, also being built at Senesco.
CBITD estimates an annual reduction of 800 tons of carbon dioxide emissions with the hybrid-electric propulsion system. The vessel’s versatility is another key feature. It can operate using a diesel-electric system, a fully battery-powered system with zero emissions, or a combination of both, providing the flexibility to adapt to various operational needs. The 164' passenger-vehicle ferry will replace an existing diesel-powered ferry, the Machigonne II, a 36-year-old 122’x37’ passenger-vehicle ferry that services Peaks Island in Casco Bay.
The new ferry, designed by Elliott Bay Design Group (EBDG), also has room for 15 vehicles. The delivery date of the CBITD ferry is also expected later this year.