Lyon Shipyard announces $24 million expansion
Lyon Shipyard in downtown Norfolk, Va., recently unveiled a $24 million expansion that includes the addition of an 820-ton boat hoist and will create over 100 new jobs.
The governor of Virginia touted the project in June, saying he was “Proud to support this expansion.” The headline-grabbing news seemed to come out of nowhere. But this expansion plan has been quietly moving forward for a decade.
Lyon Shipyard, a family-owned operation, has served the needs of the busy port since 1928. The yard which once repaired wooden fishing trawlers and steam-powered tugs now service a diverse mix of commercial and military vessels from barges and tugs to advanced military response craft. The full-service facility provides complete in-house repair, maintenance, and fabrication with over 100,000 square feet of shop space. The shipyard has grown to over thirty waterfront acres on the eastern branch of the Elizabeth River. Over the years, the business has evolved to serve the needs of the busy port and beyond. Three floating drydocks and two marine railways handle vessels up to 4300 long tons, 11 piers can handle multiple vessels pierside up to 530 feet. That was before the expansion that will add capacity for up to a dozen more projects and increase the yard’s footprint.
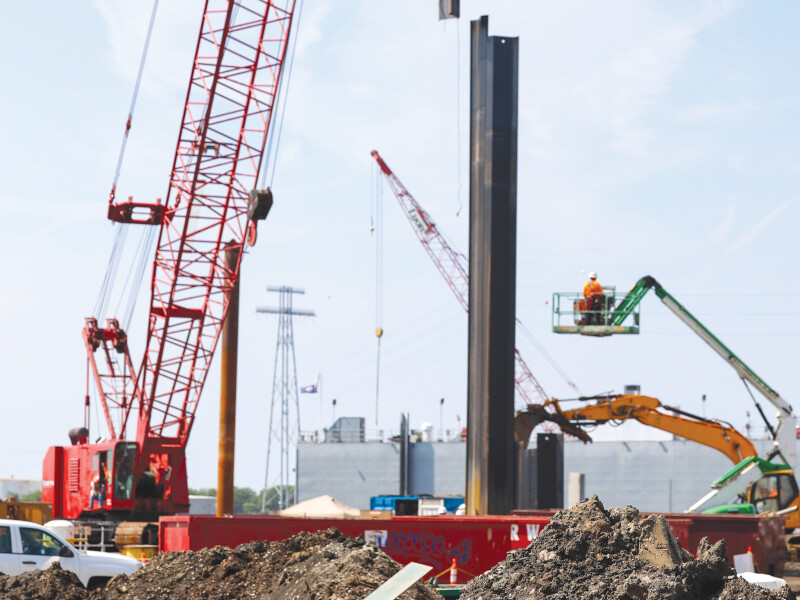
George Lyon, the president, has been at the helm of the shipyard since 1973 when he took over from his father, George Lyon, Sr. Lyon, Jr. is a keen innovator. He encourages his team think ahead and efficiently.
“We are one of the smaller shipyards in a region with a rich history in ship repair, and we use that to our advantage by being nimble and evolving along with our customers,” said Lyon.
Joshua Gerloff, project manager, said that he has walked the aisle of the WorkBoat Show with Lyon for several years and has learned from him how to look at the latest displays.
“Mr. Lyon is always on the lookout for ways to improve our productivity, so, as we walk the show, he is constantly asking, ‘Can we apply this technology at the yard,’ it is really interesting to be with him,” said Gerloff.
Back at home, Lyon tells all of the employees to consider ways that would make their jobs more efficient and maximize their capabilities. Discussions like that led to the development of a dedicated Z-drive shop.
“Our customers in the harbor tug fleet were filling our inside machine shop with their azimuth drive units. We decided if we had the dedicated shop we could work on more units and store spares to minimize downtime,” said Johnny Gaskins, VP of Production.
Lyon agree prodded the team to make sure the shop would serve not just the current generation of vessels, but whatever might be coming next. With this in mind, they added a 45-ton overhead crane to the design of the 5400 square foot shop space.
The facility is unique on the east coast giving customers the ability to have complete rebuilds or emergency repairs done completely in-house. There is room for storage of spare units so the yard can swap out and work on a malfunctioning drive without downtime for a tug.
“We can send a truck to pick up the malfunctioning unit and install a good one without having the tug come to the yard,” said Gaskins. “We have everything you need to work on these complicated drive and gear units at our fingertips.”
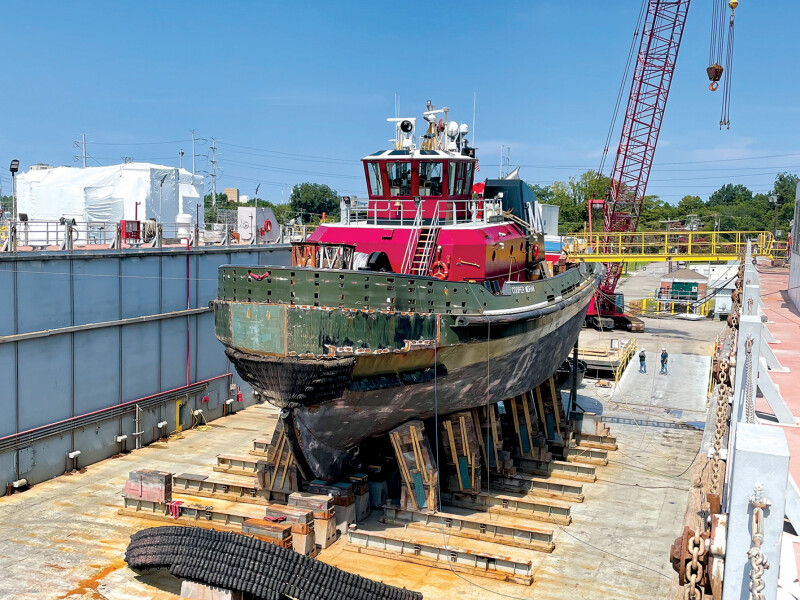
Adam Barden runs the shop. He came to the yard straight off the tugs as a licensed engineer. He has the kind of hands-on knowledge of operations to speak directly to onboard personnel to troubleshoot. He is backed up by three full-time technicians.
Last year, Lyon Shipyard signed a formal agreement with SCHOTTEL, manufacturer of azimuth propulsion systems to be the east coast provider of warranty services. This is another example of Lyon’s forward-looking vision: the agreement comes as the US east coast begins to ramp up several offshore wind projects, including one off the coast of Virginia. The vessels that install and service offshore wind turbines rely on azimuth drives and Lyon will be positioned mid-coast to provide service to them. For now, the SCHOTTEL agreement means that the harbor tugs using these drives along the coast can count on fast and reliable service. The shop also frees up the machine shops to expand their fabrication facilities, offering industrial solutions in-house as well.
George Lyon acquired the Norfolk Shipbuilding Co.’s Brambleton yard in 2007, as part of the strategic plan he developed to keep the yard competitive and sustainable in the long term. That yard and adjacent acreage form the nucleus of the ambitious expansion that will add significant capacity in the competitive repair market. The centerpiece will be an 820 metric ton boat lift.
Lyon tapped another stalwart of the Norfolk marine community, Crofton Construction Services to do the infrastructure and dredging for the redevelopment of the old yard. The old Railway #3 was removed, along with a timber pier. Crofton will construct 2-200’ concrete piers with full services to accommodate topside repair.
“My father and George Lyon’s father worked together on several projects, and it really is an honor to be part of the next chapter of Lyon Shipyard,” said Kenny Crofton.
Johnny Gaskins, reflected on the decision to build a mobile boat lift and create space for working on boats either in the slings, for emergencies, pierside at the new facility, or “on the hill.” “We spent close to a year designing this lift,” said Gaskins. “We want to be able to serve our core customers: the harbor tugs and barges as well as the military craft we bid on.”
The evolution of tug design informed the design of the boat lift. Gaskins explained that as the tug fleet converted to azimuth drives, the boats have become heavier and yet, shorter.
“You need to get the slings beneath these shortened boats that have an increased tons per foot ratio, at the same time we want to lift a standard hopper barge, and the smaller response craft.”
Lyon turned to U.S. Hoist of Center Moriches, NY in collaboration with Boat Lift, SRL in Italy to manufacture the mobile boat lift that will arrive in early 2022. The lift is designed at 95’7” long and 76’1” wide with a height of 59’10”. The lifting capacity is 820 tons. The lift will be shipped from Italy in pieces and constructed onsite.
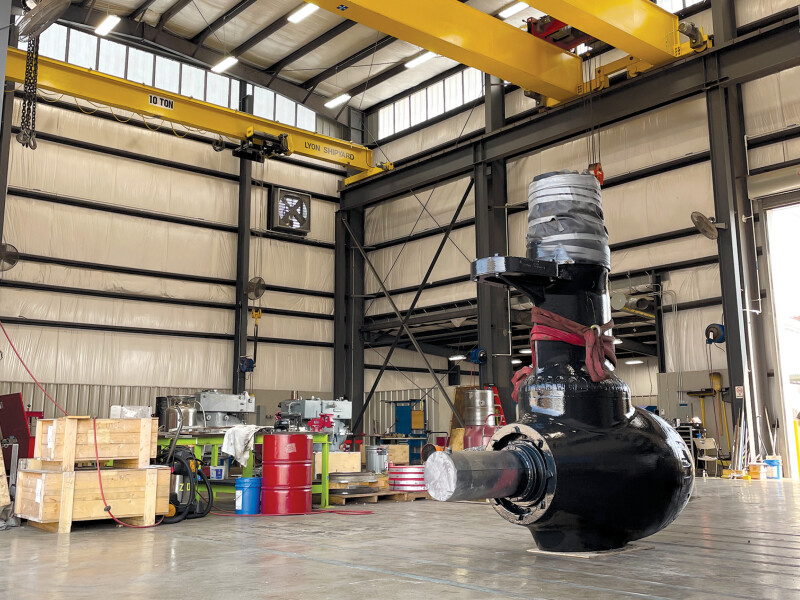
The boat lift and the added piers and shoreside space for seven vessels significantly increase capacity. “We will be able to do emergency repairs, like cutting a line out of a prop or swapping out seals, quickly, with the boat in the slings,” said Gaskins. This frees up the floating drydocks for longer-term projects.
“Lyon has maximized every square foot of the property to better serve their customers,” said Kenny Crofton.
The redevelopment of the old Norshipco yard and the new Z drive shop is part of Lyon Shipyard’s strategic plan, but it is by no means its culmination. George Lyon has his eye on the future and is already planning the next expansion. This next phase includes acquiring property inland opening up the waterfront at the original yard.
“We have very deep roots here in Norfolk and a commitment to sustaining our business of repair and service to the commercial and military fleets as they continue to grow and evolve.”
Lyon Shipyard | Main Location: 1818 Brown Ave Norfolk, VA 23504 | www.lyonshipyard.com
Lyon Shipyard is a customer-focused, family-owned and operated, ship repair facility on the Elizabeth River in Norfolk, VA established in 1928.