WorkBoat operators who are hankering for something new after years of relying on the same old diesel propulsion system often need time before making a major move in another direction. In the meantime, these operators have some diesel options to consider that won’t start to become available until the end of this year.
One of those will be part of a new MAN lineup of V12 diesels that are particularly appropriate for ferries, large pilot boats, pushboats, and larger crew transfer vessels (CTVs). Compared to MAN’s current V12 lineup, the new engines come with numerous improvements, including larger displacement, increased crankcase wall thickness, a new coolant pump, an optimized thermostat housing, a reinforced engine block, and a new crankshaft with larger bearing surfaces. These improvements make the engine “more reliable and more robust for workboat applications and increase durability before major overhauls,” said Jason Blume, sales manager, MAN Engines & Components in Pompano Beach, Fla.
The first of the new engine lineup for the workboat market will be the 30-liter displacement, 1,650-hp MAN D3872, followed by a 1,450-hp version and lastly, a heavy-duty 1,250- hp diesel. These are not spinoffs of MAN’s current V12 engine. They are based on “a completely new engine,” said Blume. The D3872 is currently undergoing field trials.
The three new engines will take advantage of MAN’s compact exhaust after-treatment system that is being used with MAN’s current V12 engines. Blume describes it as “a really great aftertreatment system.”
The new V-12 engines will be more powerful — up to 1,650 hp — but will be able to “keep the same compact modular aftertreatment system because the engines are so fuel efficient.” The MAN D3872 will be available at the end of 2024. The MAN 1,450-hp model will be out in 2025, and the MAN 1,250-hp engine in 2026. All three new engines will be certified EPA Tier 4.
More immediately, MAN’s current V12 diesel, the D2862LE, with power ratings from 1,000 hp to 1,450 hp, had been outfitted with a selective catalytic reduction aftertreatment system for EPA Tier 4, but in the past two months, a diesel particulate filter was added to the exhaust aftertreatment package, allowing the D2862LE to meet core California Harbor Craft emission requirements set by the California Air Resources Board (CARB) for vessels desiring to operate in California harbors, such as San Francisco Bay. That quickly opened California’s harbor business to MAN. “In San Francisco Bay we have some potential pilot boats and ferries” that could now be powered with the V12, said Blume. In Europe the V12 is already powering vessels along inland waterways.
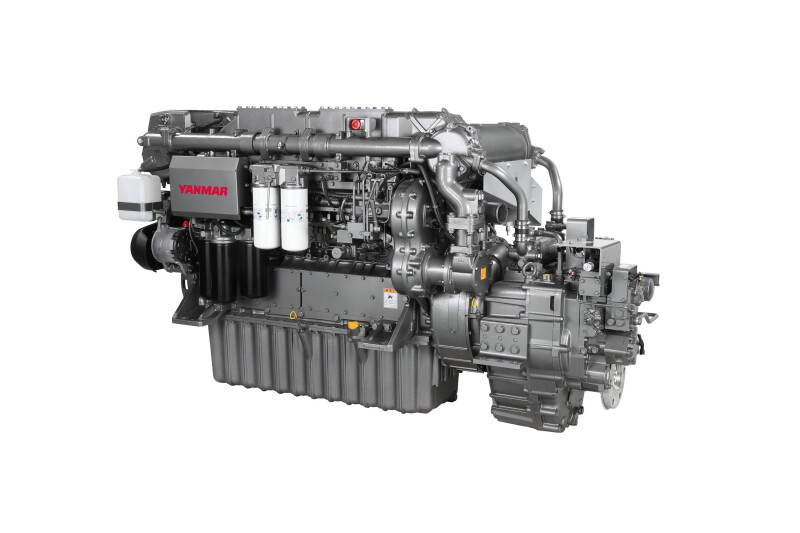
YANMAR
Yanmar is another marine engine manufacturer not content with doing what has previously been done. “It was time to upgrade technology and develop a replacement engine for our older design,” said Carl Micu, Yanmar’s division manager of power solutions. Thus, the introduction of the 6GY135W diesel with a 500 continuous horsepower rating in the 14.6-liter category, which goes up to 803 hp at the EPA Tier 3 cutoff. “We’ve not had an engine in this displacement size for a while.”
Nathan Stabile, a Yanmar marine engineer, said the new engine “is heavy duty purpose built. It’s not an ultra-light truck engine.”
Micu feels that the new engine will work well in several workboat markets, including smaller twin-screw tugs and towboats in the 1,000-hp range, as well as fishing boats and passenger vessels. For tugboats, especially, Stabile emphasizes that the 6GY135W “has a very good torque curve. It’s going to hold its rpm and hold its power where a tug typically operates — 1,200- to 1,400-rpm range.” That’s also “the best fuel consumption area for the engine.”
Serviceability is a feature of the 6GY135W diesel. For instance, the 6GY135W engine features side panels for individual cylinder heads, allowing direct access to connecting rods and crankshaft. “You can change a single kit out without having to take 97% of the engine out,” noted Micu. That reduces the amount of time spent servicing the engine.
“Side panels are new in this engine size,” added Stabile. “It makes quicker service time and lowers the cost of operation.” If the engine does have to be rebuilt, “it’s designed to be rebuilt in place, without having to pull the engine.” That, Micu said, is because “Yanmar tries to pay attention to bringing the cost of ownership down in the long run and bringing up reliability.” A multistage fuel-injection system reduces emissions by 80% with the common-rail system.
An added benefit of choosing Yanmar is the gearbox. “Yanmar is the only manufacturer to build the engine and gearbox,” said Micu. When an engine and gearbox are purchased together, “they are coupled together and tested together” at the factory. The benefit to that arrangement “is you only have to call one organization to do the service,” said Stabile.
About 20 6GY135W engines are operating in Japan. The 6GY135W should be commercially available in the U.S. and Canada in the fourth quarter of 2024. The first engines released will be IMO Tier II compliant, followed by IMO Tier III with an SCR system.
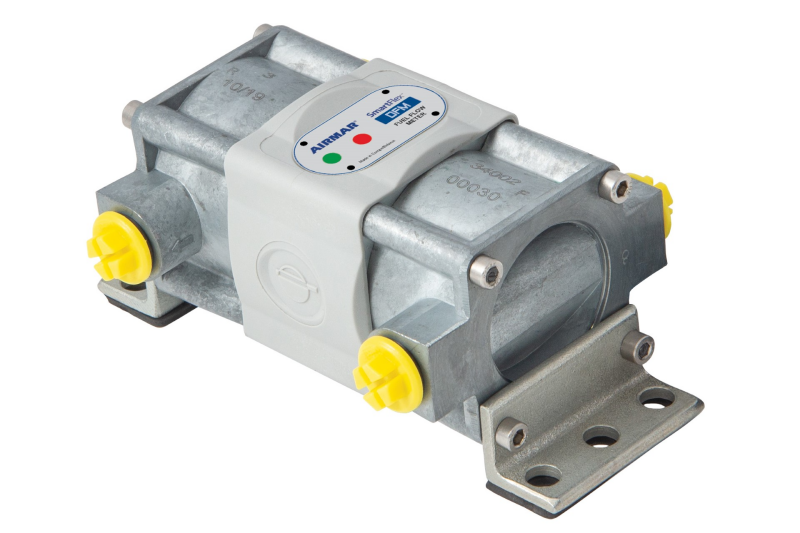
AIRMAR
Beating that fourth quarter 2024 MAN and Yanmar release date is Airmar’s digital SmartFlex Diesel Flow Meter, which was product ready in June. The sensor is designed to work with an Airmar SmartBoat Module as a single or dual-chamber flow meter with a flow rate reading from six to up to 4,000 liters per hour, depending on the model. The dual-chamber model combines measuring chambers for supply and return fuel lines in a single housing. The difference between flow rates is the fuel consumption. A single-chamber flow meter can be matched up with another single-chamber flow meter for fuel burn and consumption data.
Airmar’s fuel-flow sensor is a kind of slip-ring technology made up of
a pivot post and around it a ring. “As the fuel enters the chamber, it turns the ring,” said Airmar technician specialist Zack Floyd. “It’s very difficult to clog and is highly accurate, within 1%, because of the way it senses the rotation of the ring.”
The Airmar SmartBoat Module “is the gateway” for the fuel sensor’s flow data, first interpreting the data and “then pushing it out to NMEA 2000,” said Floyd, making it accessible on various displays. Installation is nearly effortless, requiring no hardwiring. “It takes three minutes to set up. It’s all done through the SmartBoat box (module).”
The fuel flow information includes instant and total fuel consumption. This should be especially meaningful to workboat operators “that want to bring older engines into digital and see the actual fuel consumption and want the real-time burn. This will allow them to do that,” Floyd said. “Knowing how much fuel they consume, they can determine how far they can go and have enough fuel to make it back.”
With newer engines, fuel consumption is calculated. The engine computer knows how much the fuel injectors should be sending and can adjust the fuel volume based on load, and the amount of air and rpm. “The problem is,” said Floyd, “you are relying on the computer to calculate that, and the assumption is all systems are good and working in an ideal spot.” But if there’s, say, a leaky injector, “and the leak is pushed into the exhaust and shot out the back of the boat, you never know that” because the computer doesn’t measure the supply rate and how much fuel comes back to the tank. “You have no real way to know the efficiency at a given rpm because the margin of error is so high.”
Airmar’s digital SmartFlex Diesel Flow Meter with 1% accuracy rate allows vessel operators to save money by modulating the rpm based on load conditions, speed, or tidal conditions. “Lowering the speed two knots, you can save five to 10 gals per hour, $20 to $30 an hour by dropping the boat speed two knots,” said Floyd, as an example. “The accuracy of the flow equates to money-saving every hour.”