Before an offshore service vessel can resume normal service, all overdue class and statutory surveys must be completed. Also, accurate running hours for machinery should be made available throughout the lay-up period so that appropriate spares for the maintenance of machinery items at reactivation can be planned by the joining crew and any attending technicians.
Full consideration of the lay-up reports and log books should enable a formal reactivation plan to be developed to restore the engine room machinery and power systems to full working order.
Planning for reactivation should of course commence when vessels are first laid-up and therefore determining the reactivation of any OSV depends largely on the preparations made for lay-up – or lack of them – and the engineering and maintenance approach taken during out of service periods. From an engineering perspective, there are several fundamental factors that need to be considered that can considerably influence the chances of an orderly return of a vessel to normal operation.
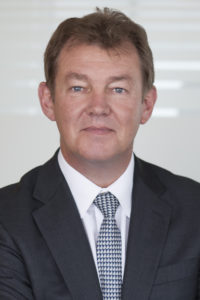
Neil Graham
The risks of engine, component and associated system damage during lay-ups are many and varied, including the potential for corrosion, spalling, fractures, abrasive wear, adhesive wear, porosities, seizure, fretting and cavitation. The possible deterioration of the lubricating oils and fuel oils during the lay-up period also requires proper consideration. Lubricants and fuels are normally hydrocarbon-based products that are subject to degradation and contamination over time which poses a risk to the efficient and safe operation of engine parts.
Routine checking and testing of all lubricating and fuel fluids should therefore be undertaken ahead of any propulsion and generator system reactivation work, including the inspection, cleaning and renewal where required of all cartridge and centrifugal filters. The impact of the presence of moisture and any impact on engine parts is another area of concern and the review of any dehumidification records during lay-up can also provide a pointer to the likely risks of corrosion-related problems.
It is assumed that if the engines have been in cold lay-up, major overhauls (complete or partial to satisfy surveyors and maintenance requirements) will be conducted. Therefore, tasks such as flushing through oil galleries will be done when the engine has had bearings etc. removed.
With the main engines, the current advice from engine manufacturers is for main engine crankcase spaces to be closed up and dehumidified during lay-up. However, this is not always the case and the recommended course of action is for a full crankcase inspection to be carried out, alongside checking the condition and security of rotating parts.
The pistons and cylinder liners should be protected with an inhibitor and regular crankcase inspections carried out to check general condition of engine internal components. Blanking off the exhaust gas system and air intakes is recommended to prevent moisture ingress into the engine.
For the lube oil system, consider blanking off or disconnecting the vent lines in the engine room. The LO pumps and priming pumps should be turned on a regular basis and run up prior to starting the engine. Purifiers should be run up to clean the oil as much as possible, with samples taken for analysis before starting the engines.
Ideally the lube oil system should be flushed through with a recommended flushing oil prior to starting the lube oil pumps.
Fuel lines with residual fuels should be drained and flushed with MGO prior to lay-up. Any fuel remaining on board should be regularly tested for water, sediment, abrasives and microbial activity in the case of distillates. Water in fuel tanks should be drained off on a regular basis.
Fuel injection valves should also be cleaned, adjusted and refitted, and this requirement often applies to the fuel pumps also. The engine fuel system should be circulated prior to engine starting to ensure there is no leakage.
It is also recommended that the starting air system is drained and opened, cleaned and left dry while sea water systems, including pipelines and heat exchangers should be opened and drained of water, with the heat exchangers being flushed with fresh water before being cleaned. If possible, leave the SW system open to benefit from the dehumidified air.
Fresh water systems can be left filled if the appropriate chemicals are added and regularly tested to prevent corrosion and settling of solids.
In general, all valves in all systems to have spindles greased and valves operated regularly to prevent seizure. Note that this also applies to ships' SW inlet valves but a blanking off of the SW system must take place to prevent SW ingress.
The engines should be rotated regularly and the shafts should be returned to a different position each time.
A vessel’s auxiliary diesel engines may also have already been in need of overhaul at the time of going into lay-up. This is particularly the case if they had been run at low loads for months during any period of interim hot lay-up without appropriate maintenance being carried out or running hour logs properly kept. It is therefore important that these items of machinery are also carefully examined as part of the reactivation process.
If the auxiliary engines have not been run during the lay-up period, a sample of main bearings and connecting rod bottom end bearings should be opened for examination, with further examination and possible remedial attention being dependent upon the condition found.
On completion of the various commissioning tasks that are undertaken after all checks and maintenance activities have been completed, full load engine and generator tests will be necessary to fulfill the requirements of the owner and the class surveyor.
Neil Graham is the technical director at U.K.-based diesel power specialists Royston Ltd.